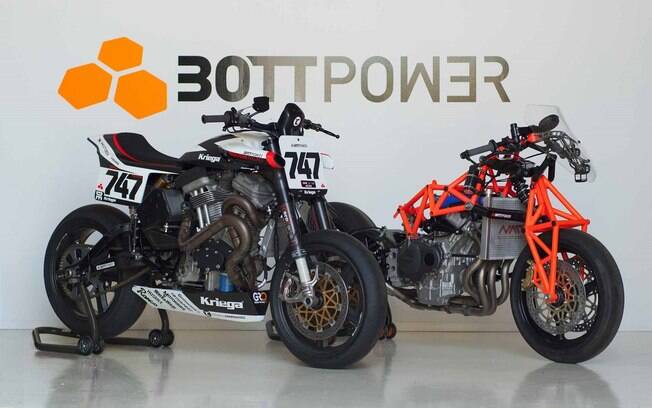
A Bottpower, empresa espanhola de motocicletas, mostraram imagens de um componente de titânio para seu novo modelo esportivo, usinado em impressora 3D. A peça serve para dar suporte aos faróis, à câmera GoPro que vem equipando a moto e à bolha. Mas o mais impressionante nessa história não é a peça em si, e sim o processo para a fabricação, que propõe novas tendências para a indústria de veículos. David Sanchez, dono da empresa, disse ao site inglês MCN como foi o passo a passo.
LEIA MAIS: Eis o primeiro carro elétrico feito a partir de impressão 3D
O primeiro passo, antes da impressora 3D , foi fazer um estudo das principais cargas que o suporte da motocicleta esportiva deve suportar. As cargas aerodinâmicas foram calculadas com modelos de CFD no software Virtual Wind Tunnel do Altair. Foi criado um túnel de vento virtual e um para-brisas virtual foi colocado dentro dele, para aferir a carga aerodinâmica da moto em 186 mph (299 km/h).

Depois disso, os projetistas puderam desenhar o volume externo máximo que o suporte poderia ter. Então, usaram outro software, que realizou os cálculos das cargas aerodinâmicas e recortou o máximo de material possível para obter uma boa relação entre rigidez e peso. Após isso, o design foi suavizado para uma forma mais limpa.
Você viu?
LEIA MAIS: Curtiss revela nova moto elétrica "V8", com 217 cv, que chega nos EUA em 2020
Uma vez que a forma foi confirmada, o braquete foi construído em outro programa para uma análise de todas as cargas para se garantir a procedência. Por fim, o formato foi enviado por email para a impressora Optimus 3D, que o imprimiu. E foi nessa próxima fase que se observou, em ação, a tecnologia que promete se popularizar no futuro.
Novos paradigmas da engenharia
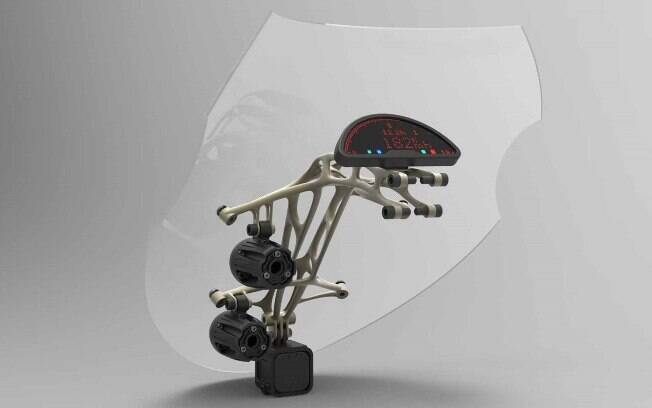
A impressão 3D em titânio é um processo muito diferente do plástico de se trabalhar. Um laser de alta potência derrete a poeira de titânio em pontos precisos para moldar a forma. Então, ela é construída em camadas, com as barras postas por baixo que agem não só como um suporte, mas também como um dissipador de calor, para ajudar a resfriar a peça à medida que é usinada. Quando pronto, o componente é cortado e furado, conforme o esquema previsto para o projeto.
LEIA MAIS: Confira a lista das 5 motos trail mais em conta de cada marca, que valem a pena
Entre as montadoras maiores, a BMW foi uma das que se aventurou com a nova tecnologia, produzindo um quadro S1000RR inteiro através de impressora 3D . Essa “ferramenta do futuro” promete poupar o tempo de muitas indústrias, uma vez que a usinagem das peças é feita mais rapidamente e exatamente do jeito que os engenheiros quiserem, sem aumentar os custos. O maior desafio será, talvez, de assegurar igual durabilidade.